Technology
Bag-On-Valve (BOV) vs. Classic Spray Technologies
What does TUNAP stand for? Innovative, sustainable solutions with a focus on health, quality, and environmental compatibility. Discover our cutting-edge Bag-on-Valve (BOV) aerosol technology, used in technical products like airco well® 996/997 and cosmetics, reducing our ecological footprint while delivering top performance.
Reading time: ca. 6 min. | An article from Dr. Sabine Riha | TUNAP Blog
What does TUNAP stand for? We inspire our customers with sustainable developments and system solutions in the area of chemicals. Our aspiration is to deliver the best quality and, at the same time, fulfil the highest standards with regard to health and environmental compatibility.
Among other things, we realise these quality, health and environmental ideas with the sustainable Bag-on-Valve (BOV) aerosol technology. This is used in our technical products and also in the cosmetics industry. For example, our air conditioning system products airco well® 996 and 997 are using BOV technology. Other products are in the pipeline.
The BOV system is not only an excellent spray dispensing system, the sustainable packaging process also helps reduce our ecological footprint.
The difference between conventional aerosol technology and the BOV system is that with the conventional variant the product and propellant are in the can together with no separation (see figure). With BOV technology, the propellant and the product are separated in the can.
The active ingredient is contained in a separate flexible bag, which is connected to the valve, and the compressed gas is in the remaining space between the bag and the side of the can. When the spray nozzle is pressed, the pure product is dispensed but not together with the propellant as is the case with traditional aerosol cans.
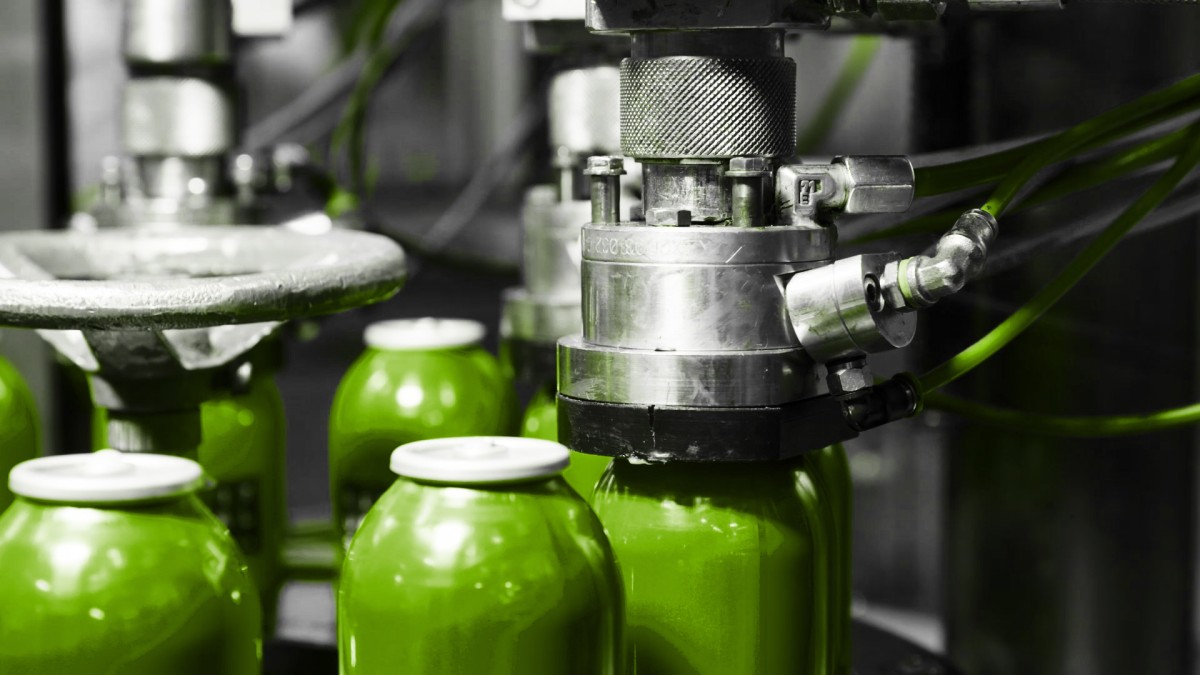
Four steps are required to fill a product into a BOV can.
Step 1
A valve with a welded-on bag (BOV) is placed in the can.
Step 2
The entire volume is then filled with compressed air and closed.
Step 3
Pressure check
Step 4
The active ingredient is filled into the bag through the valve. The pressure in the can increases due to the volume displacement. Then, the spray nozzle and lid are placed on top.
- Because the product and propellant are separated, BOV technology has several advantages over conventional aerosol spray technology. One of the main aspects are the safety and environmental benefits. This is because no flammable propellants are needed, just environmentally friendly gases like air or nitrogen. Wherever possible from a technical aspect, TUNAP also uses environmentally compatible propellants in many of its conventional aerosol cans.
- BOV technology also opens up new technical possibilities for TUNAP. For instance, BOV offers solution approaches for special problems in the low VOC (volatile organic compounds) area and is an option for manufacturing aerosols with higher pressures (high-pressure aerosols), such as for cleaning air conditioning systems. Compared to conventional aerosol cans, BOV also offers a solution for products that are difficult to fill with compressed gases, such as non-polar or viscous ingredients.
- The bag inside the can guarantees 100% separation of product and can, which means that Bag-on-Valve could be used for sensitive and aggressive products, such as cleaning products in areas where fuels are used.
- In addition to the special benefits of BOV technology compared to conventional aerosol technology described above, the general advantages of packaging products in aerosol cans also apply. For instance, BOV packaging is a hygienic and reliable form of packaging. The aluminium bags ensure that the formulation is hermetically sealed. This prevents contamination and oxidation of the active ingredients to the last spray, which also contributes to the durability of the products. This also means a reduction iof preservatives.
- The products are easy and convenient to use, just like conventional aerosols. The product can be used multiple times and be almost 100% used up. The materials used can generally be recycled.